Kristina(Kicki) Volcini began a journey 25 years ago in the warping hall at Svensson, the company where her father Bo Johansson worked.
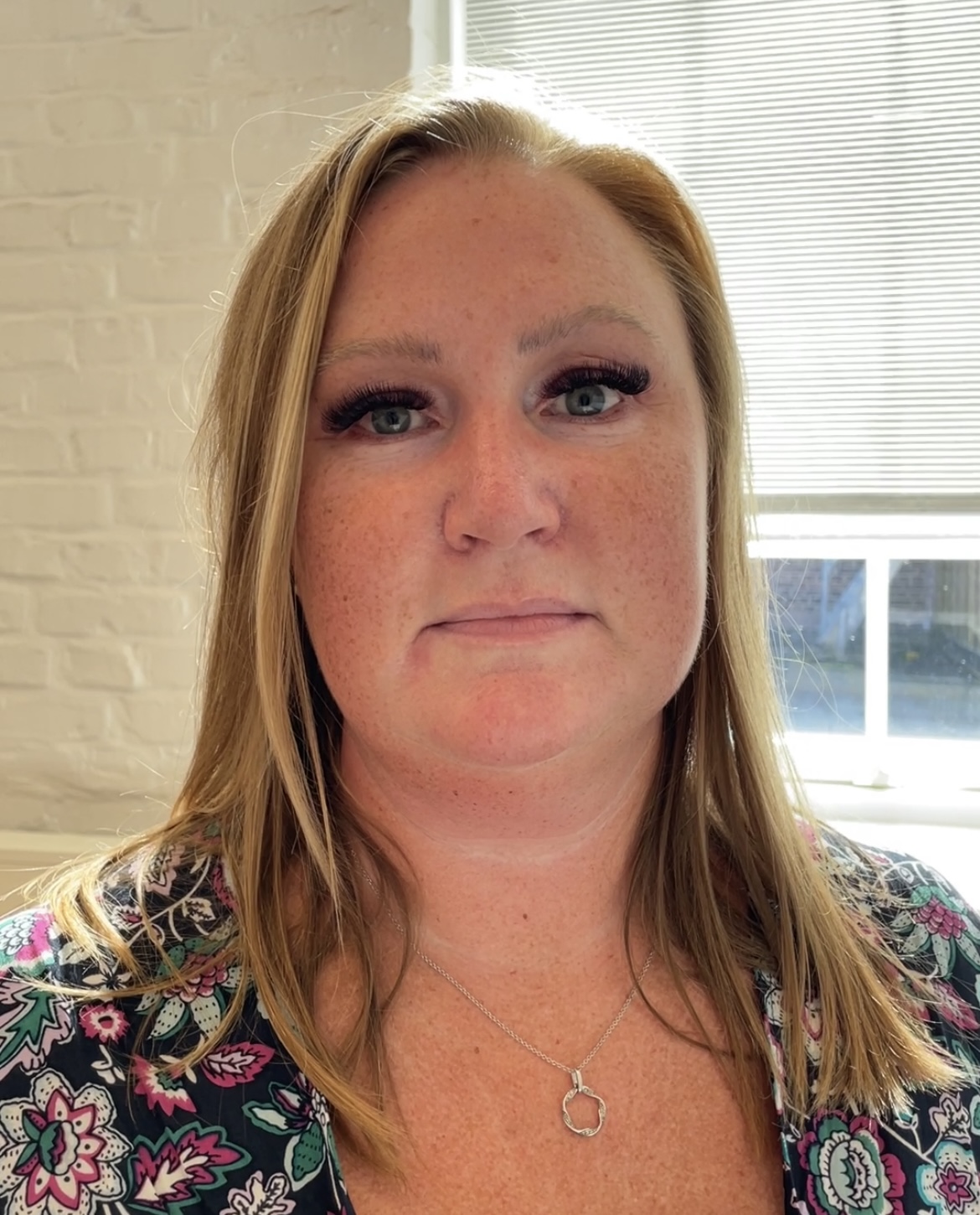
Kristina (Kicki) Volcini is Svensson's Lean Transformation Leader and trains staff all over the world
She perhaps might have guessed that one day a son of her own (Simon) would be driving forklift trucks of yarn around the factory floor as she once had.
She might also have guessed that if she worked hard, she could become a team leader, as she did in 2013. And then go on to be a shift leader (2017).
But in 2019, Kicki was involved in a car accident which turned her world upside down. Suffering from whiplash injuries, she was sjukskriven and stuck at home.
“It gave me time to think,” she remembers. “It had always been my plan to study after a few years in the workplace but life came in between,” she says.
“I was given leave of absence and I enrolled at the University of Borås,” she says.
“I remember sitting there on my first day at the University of Borås. It was very exciting and I was quite nervous that I’d be very alone, being 18 years older than the other students. But they were all very welcoming,” she says.
In 2022 Kicki qualified as an engineer and today its her job to see that a culture of efficiency and excellence permeates the Svensson workplace from Estonia, to North Carolina and the factory floor at home.
“I’ve trained the teams in the US, in Eastern Europe and I’m about to head off to Netherlands as well,” she says.
“Lean is about effectiveness,” she explains. “At Svensson it can mean, for example, that the vehicles we use are maintained so that everything is in first class condition,” she says. “Or how we log every slight fault in the knitting and weaving and seek to always improve.”
Today it is part of Kickis role to ensure that climate screens and interior textile orders are fulfilled as efficiently as possible.
“When Toyota developed the first Lean Transformation ideas in Japan, they had a goal to have their products sold and paid for before they rolled off the production line,” she explains. “Today, they’re still known for best in class quality standards.”
What is a Lean Transformation Leader?
What today is known as Lean Production was originally developed by Taiichi Ohno, an industrial engineer and executive at Toyota. Influenced partly by Henry Ford’s car making ideas, he developed the Toyota Production System.
Lean Production analyses the flow of energy and movement in a workplace and looks for any waste. It includes the concept of continuous improvement (kaizen) and is known as the source of Just-in-Time logistics, where inventories are kept lean and filled only when needed.
5S grew out of the Toyota system and is a framework for ensuring the workplace is clean, efficient and safe.
“Sortera, Systematisera, Städa, Standardisera och Se till are the 5S,” says Kicki Volcini.
”It’s an approach that has made a huge difference at Svensson over the years since I started here.”
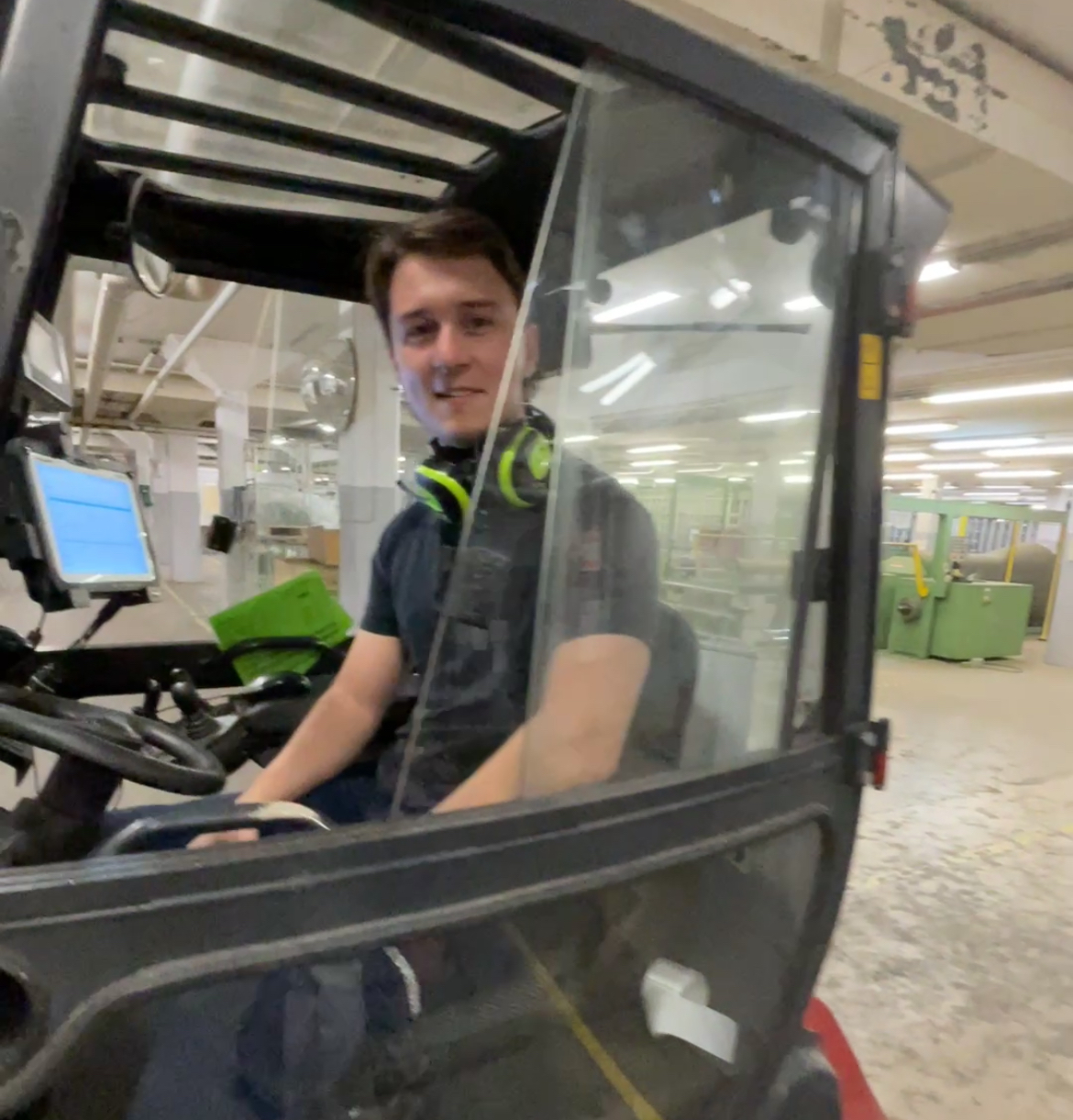
Simon Avramsson, Kicki's son
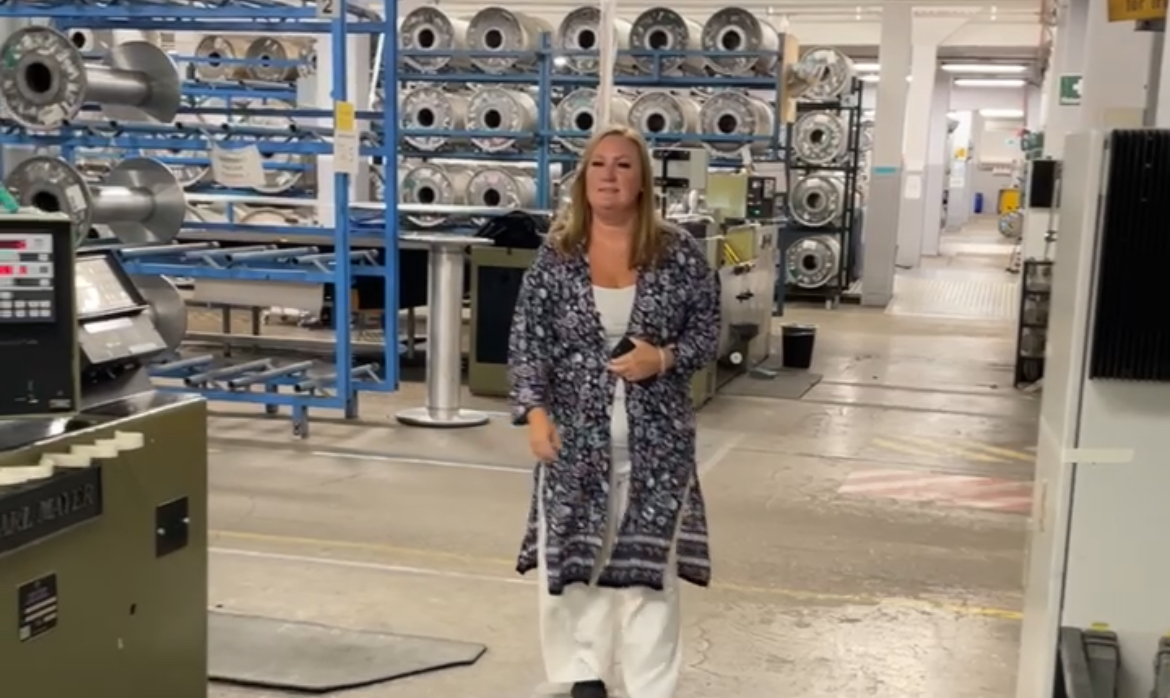
Kristina in the warping hall
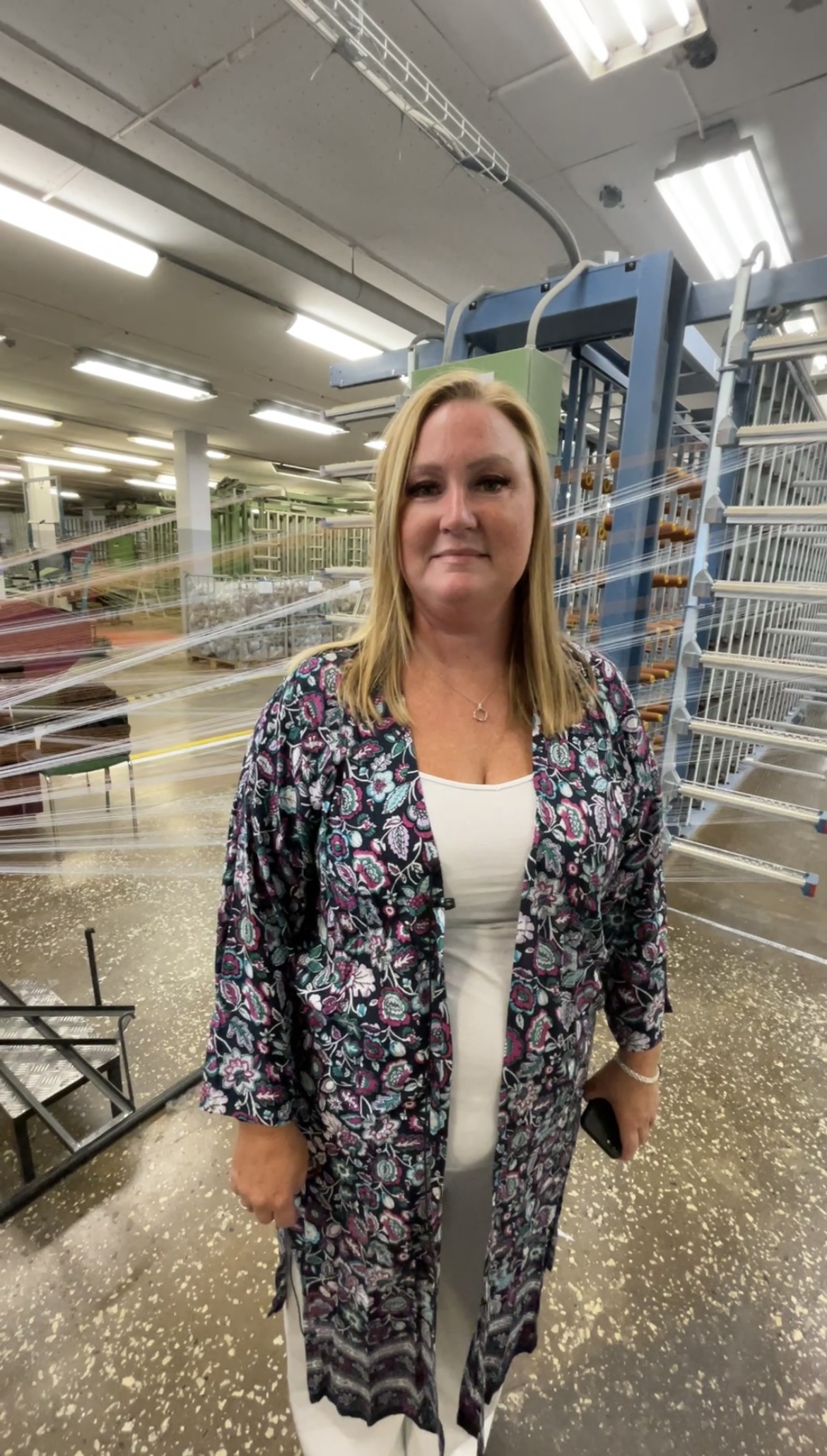
The floor where her journey started 25 years ago