Cleaner installation. Better greenhouse yield
Could a single dirty air event during screen installation really cost a new greenhouse project hundreds of thousands of Euros in lost yield over the following eight years? Here are 5 steps the best installers and growers use to keep their climate screens clean and their new greenhouse productive for years to come.
Energy screens have been a game changer in commercial horticulture. Today it is common for growers to be able to cut their energy bills in half or more by choosing effective screen technology. But to be able to deploy them to enjoy those energy savings, the screens must admit as much light as possible. And that means taking extra care to avoid contaminating the screens during greenhouse construction.
Avoid installing screens at times of poor indoor air quality
As those who visit greenhouse constructions sites know, things can get pretty dusty and unpleasant, particularly in warm, dry conditions.
In tests, we found that contamination of greenhouse energy screens with construction dust and ground dirt can reduce light transmissivity by nine percentage points.
That’s a problem. Svensson’s Its high transmission of light makes it ideal for growing light-demanding crops like tomatoes, peppers and roses at much-reduced levels of energy consumption.
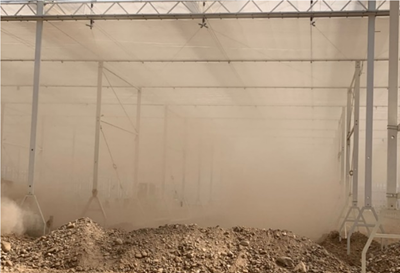
High levels of particulates in indoor air will also find their way onto textiles, which can reduce the effectiveness of functional materials
Because the thread is in contact with the air, the filaments that make up the thread in the screen can wick away excess moisture. The pattern also creates a ripstop strength that is important to the structural integrity of the screen during its daily deployments and retractions.
But like the human lung, the screen is vulnerable to the particles thrown up during construction work.
So what exactly can be gained by keeping the a screen installation clean?
And what might the cost be of contamination in terms of lost production?
Best practice
There are of course fantastic examples of greenhouse environments which seem to approach surgical standards of cleanliness.
Svensson’s various partner installers and greenhouse constructors carry with them decades, generations even, of experience in exactly how to keep things white and fresh on opening day.
We spoke to installers to find the key steps they take the assure a clean screen installation. These are simple, important measures that will ensure your equipment performs best, allowing you to reap the full return on your new investment.
Testing the impact of construction dust on energy screen
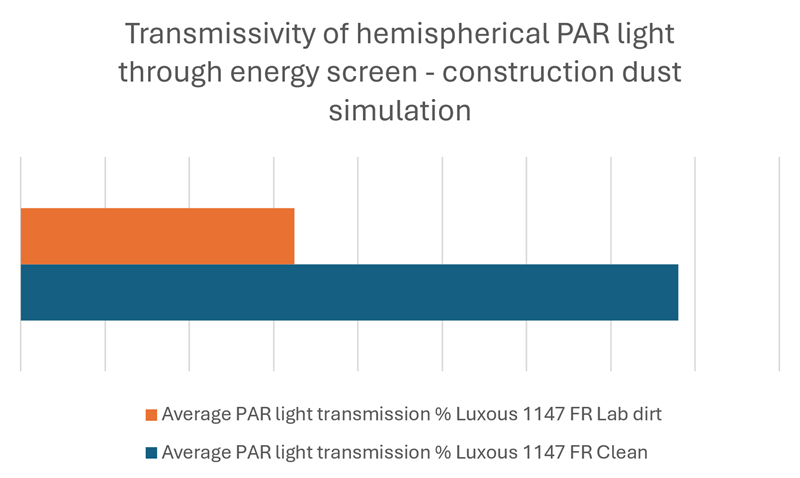
There were dramatic differences discovered in the light transmission performance of two samples of Luxous 1147 energy screen.
Red-brown pigment was applied with a dry paintbrush to a new screen to simulate an energy screen exposed to dirty construction site conditions. We called this sample the “lab dirt” sample.
A clean and new screen was also tested. We found that the lab dirt sample transmitted 9.1 percentage points less PAR light compared to the clean screen.
In absolute terms, the loss of transmissivity equates to 12.04% less PAR light reaching the crop. This is a large impact.
When we imagined a newly built Dutch beef tomato greenhouse project of 4 hectares, we projected that that at recent produce prices, a Dutch grower could lose Euros 153,000 a year in yield*.
Over the eight-year life-span of a climate screen, the cost would likely pass one million euros.
* For our example, we imagined that in temperate conditions, the screen is fully deployed for 12 hours each day, halving the light reducing impact of the contamination on the screen. We multiplied the resulting percentage reduction in light (6.02%) by 0.7%, which is the lower end of the range of impacts on tomato yields known as the 1% rule. This gave a yield reduction of 4.215%. We assumed a wholesale tomato offtake price of Euros 1.30/kg.
Yield is reduced by 3kg/m2 to 67kg/m2 annual yield. The anticipated total yield falls from 2.8 million kg to 2.56 million kg. At a projected offtake price of 1.3 euros per kilogram, total sales will be reduced by Euros 153,426 each year.
5 vital steps that keep your new climate screens clean
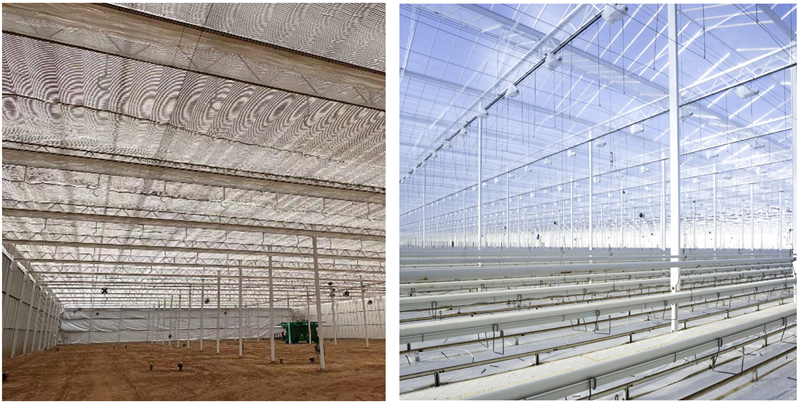
Striking comparison: In the picture to the left, the screen has been installed before ground cover and much more airborne particulate has reached the screen above. In the picture to the right, a pristine installation carried out by Peter Dekker Installaties (PDI) at Schenkeveld in the Netherlands shows what can be achieved when the actual screen installation takes place during the clean Finalization phase close to project delivery and first planting.
Take these five steps to assure the performance of your energy screens, and the long-term productivity of your greenhouse.
1. Make sure your screens arrive at a clean storage space and are kept clean
From the moment the delivery is scheduled to arrive, see to it that the screens are kept clean, elevated above ground level, and covered to protect them from dirt and dust. Best practice is to keep the screen in a separate packing hall until installation time.
2. Schedule the installation for when the indoor air is cleanest
Let’s face it, the indoor air of a construction site can be pretty dirty. Think of when you last visited a house or apartment that was being remodeled. There is a dirty phase of removing walls, making concrete, installing pipework. Then there is a cleaner phase.
Best practice is to pull in or clip in the screen when the building phase is complete and the greenhouse, glass, trellis and wiring has been cleaned and, where possible, floor cover has been applied. The air quality in the greenhouse should now be perfect.
3. Employ water dust suppression just before screen installation
If it is not possible to schedule screen installation after ground cover or flooring is installed, ensure that dust suppression using water is carried out immediately before screen installation. This also applies to greenhouses with full soil cover, such as for Chrysanthemum.
Remember that in hot conditions the floor will dry out quickly, so schedule your dust suppression effort to take place as each new section is installed.
4. Ensure you include a clean “Finalization Phase” of construction in your contracts and your building site meetings
It is best practice for contracts to call for a schedule of work divided into a dirtier building phase and a later clean phase of work, sometimes called the Finalization Phase.
It is important that light transmissive greenhouse shade screens are not installed early during a construction project to provide shade for the building site workforce.
Once cleaning is complete and groundcover or flooring is installed, no further dirty work should be carried out.
5. Sequence multiple screen installations to provide protection to the most light-transmissive screen
If you are installing a blackout screen like Obscura, this screen will not be impacted by dirt and dust like a screen that has been designed and manufactured to admit as much light as possible.
This presents an opportunity. If you can schedule the installation of the multiple screen system so that the blackout screen is installed first, it can double as a dust protection layer, preventing dust settling on your more dust-sensitive and light transmissive energy screen.
How a clean greenhouse installation looks when everything goes right
Red Harvest has been growing fast these last 30 years since its beginnings in De Lier in the Westland region of Netherlands. The company chose to expand in the north in Middenmeer and expects to have 50 hectares under production of tomatoes and cucumber by 2025. Greenhouse No 5, pictured here, is one of six 7.5 hectare blocks on Red Harvest land and was completed in May 2024.
At Svensson, Johan Weesie, documented progress from the initial frame construction, to the preparation of the trellis to receive Svensson screens and then much later their installation.
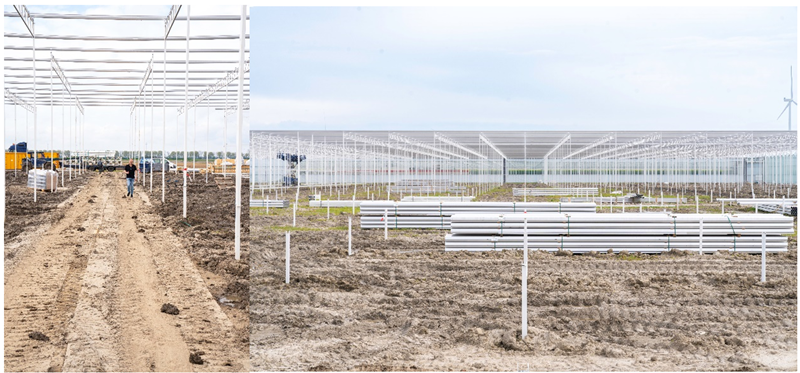
The Construction Phase of the project. At this point, the screens themselves should be stored away from the site to keep them clean, but the trellis has been prepared for them during this stage
“Everything was done so nicely and so cleanly,” he says. “Like a bride’s dress on a wedding day, there was this impressive feeling of pure whiteness,” he adds.
He says that on each visit he was impressed by a feeling of a well-run and orderly site: “The construction meetings were so well done. They were also careful to follow up each stage to ensure that things were done as planned.”
“For us it was a pleasure to watch because there was clearly no contamination of the screens, and the installation was done exactly as we would hope to see.”
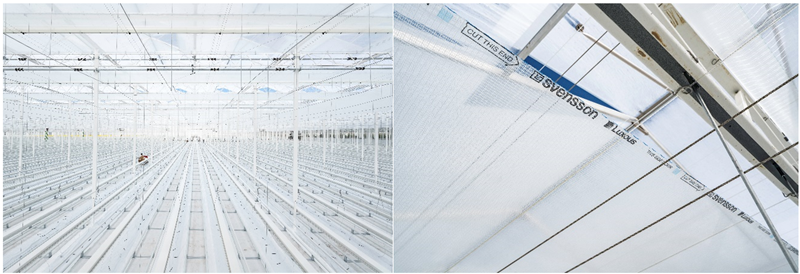
Now the screen has been clipped into place in this textbook installation at Red Harvest. With just days to go until first planting, the contractors are careful that no more dusty work is carried out, and even dirty boots are frowned upon now
Ramon Bol is sales director at screen and net installations specialists Alweco. The company carried out the installation of the Svensson screens.
“Construction began in October, 2023 and it was delivered in May and it looked terrific,” he says. “I’m very proud of the end result and that Alweco was chosen to work with Red Harvest.”
“Everyone has the same goal, the growers certainly want a clean delivery,” says Bol. “At the start, when we are talking about money and contracts, cleanliness is also one of the goals in these discussions!”
In the Red Harvest project, the screens were traditional clip-in systems and Alweco carried out the technical installation in the trellis early in the project, leaving the screens themselves for later installation.
“A large part of our work is done before the concrete workers and other contractors come in.”
When it’s time to install the screens the Alweco team comes back. The entire greenhouse has been cleaned ahead of the groundcover being laid. Now, there may be just 14 days until first planting.
“At this stage the concrete is finished, the heating pipes are in, the groundcover is laid and from this point on there is a common understanding that all the contractors are focused on delivering a clean new greenhouse,” he says. “At this point, dirt is kept out, even muddy boots must not enter.”
The Alweco team work from hydraulic scissor lifts that run on the heating pipes, so the groundcover is not disturbed.
Learn more about construction hygiene and leveraging the fantastic benefits of Svensson screens
Planning to install climate screens in a new-build? Book a free consultation to explore options to keep your screen in top condition. Don’t hesitate to call us, even if you’ve not yet decided to choose Svensson for your project.